WIRTGEN sensors and scanning equipment
The transducers
Deviations from the target value are
picked up by the sensors and calculated by the levelling system, which
then automatically transmits a corrective value to the machine.
Different sensors are used for different applications depending on the
reference used (e.g. pavement surface, kerb or stringline).
The sensors are generally available for all product divisions and machine types and are used to suit the specific application
Laser sensor: With laser levelling methods, laser sensors on the machine receive signals from a rotating laser beam.
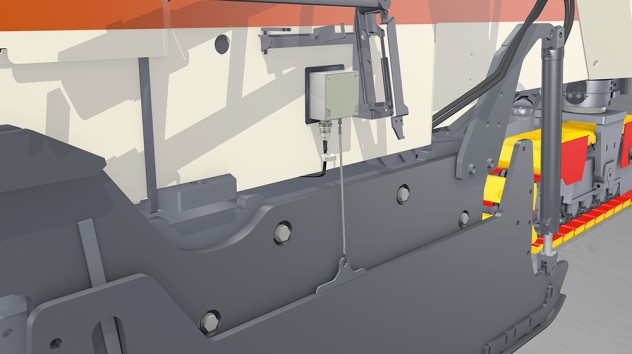 |
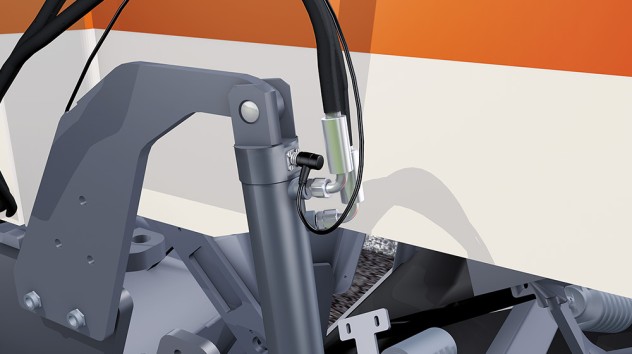 |
Cable
sensor: A mechanical cable sensor connected to the side plate with a
wire determines the difference between the side plate and machine
chassis. |
Hydraulic
cylinder sensor: Path sensors in the hydraulic cylinder determine the
difference between the side plate and machine chassis. |
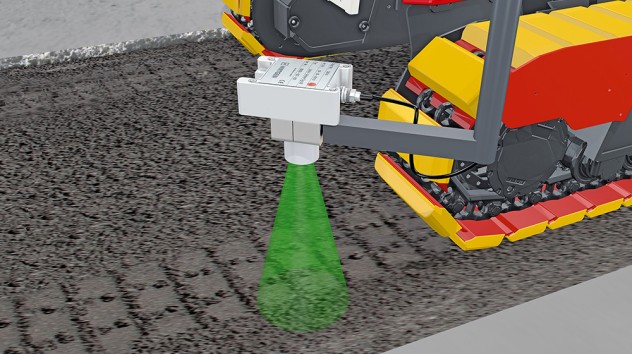 |
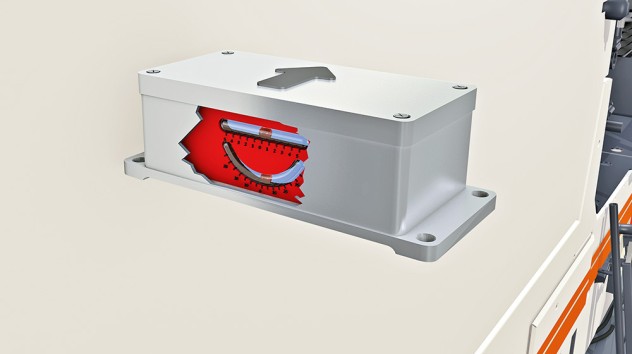 |
Ultrasonic sensor: The non-contact ultrasonic sensor determines the distance of the machine to the reference surface. |
|
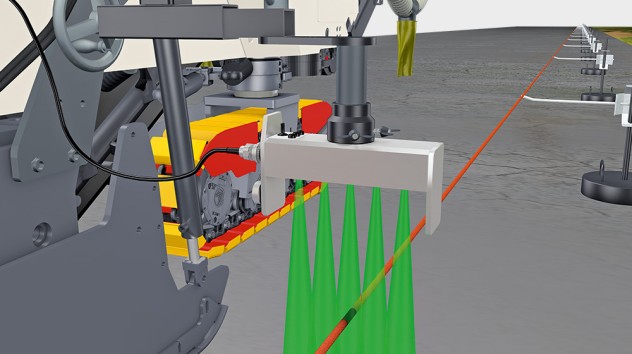 |
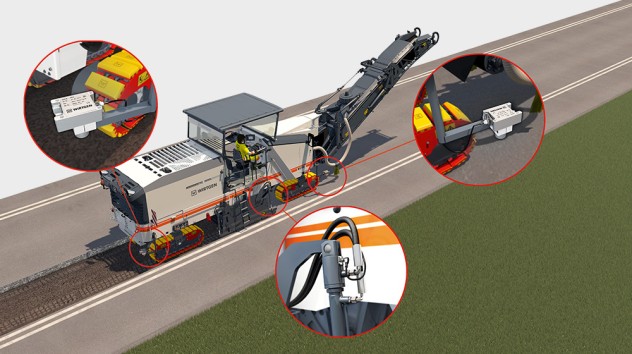 |
Sonic
Ski sensor: The non-contact Sonic Ski sensor determines the distance of
the machine to the reference surface. This may also be a stringline. |
Multiplex
systems: Multiplex systems combine multiple sensors on one or both
machine sides (e.g. cable, ultrasonic, cylinder sensor). Using the
average value of the connected sensors, the current milling depth is
calculated with high precision. |
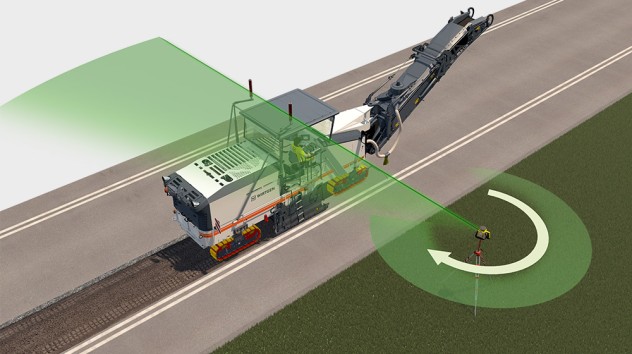 |
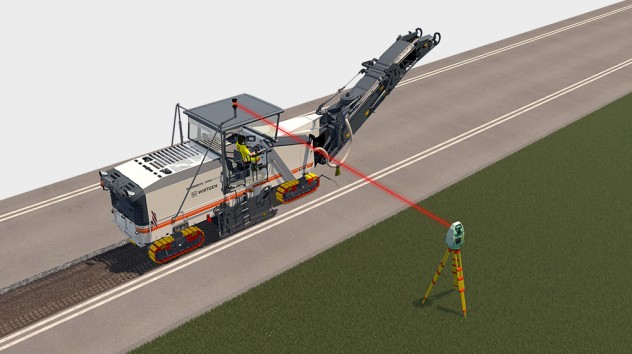 |
> Laser sensor: With laser levelling methods, laser sensors on the machine receive signals from a rotating laser beam.
|
3D
sensor: A total station focuses a receiver prism, from which it
calculates the position and height of the cold milling machine. This
data is transferred to the 3D computer for further processing.
|
Công nghệ khác
WIRTGEN levelling systems